Client
Offshore oil & gas regulator
Asset
FPSO
Overview
The client requested a ‘health check’ of an FPSO within their jurisdiction. A special verification activity was conducted to assess the current condition of the asset integrity of this FPSO and assess the effectiveness of the maintenance management system. This verification included ensuring compliance with regulations, codes, standards, original equipment manufacturer recommendations and reliability/availability targets as prescribed in their installations’ safety case.
The main elements of the health check are the primary structure, process systems, safety systems and electrical equipment. Examples of activities carried out during the health check are:
- Conducting a special verification activity to assess the current condition of asset integrity of the FPSO.
- Assessing the effectiveness of the maintenance management system in maintaining the asset.
- Assessing compliance with regulations, codes, standards, original equipment manufacturer (OEM) requirements.
- A review of the reliability/availability targets as prescribed by the Installations’ Safety Case.
- Verify Process safety.
- Structural and electrical assessment.
For each of the Safety and Environmentally Critical elements included in the 'health check', we determined the degree of compliance with the requirements in the installations' Safety Case.
How we helped
Through our assessment of the safety critical elements on the FPSO, regulatory compliance with codes, standards and original equipment manufacturer requirements were determined. Assessing compliance enabled the owner of the FPSO to improve protection of Safety and the Environment.
The costs and interruption of the FPSO's operation was kept to a minimum by reviewing documents onshore and assessing the findings offshore. This reduced roughly 1/3, or 800 hours, of the man hours offshore. For example pressure safety valves were frequently identified without the leak detection pipe installed or visible. The degree of compliance with the requirements is displayed through a colour coding system:
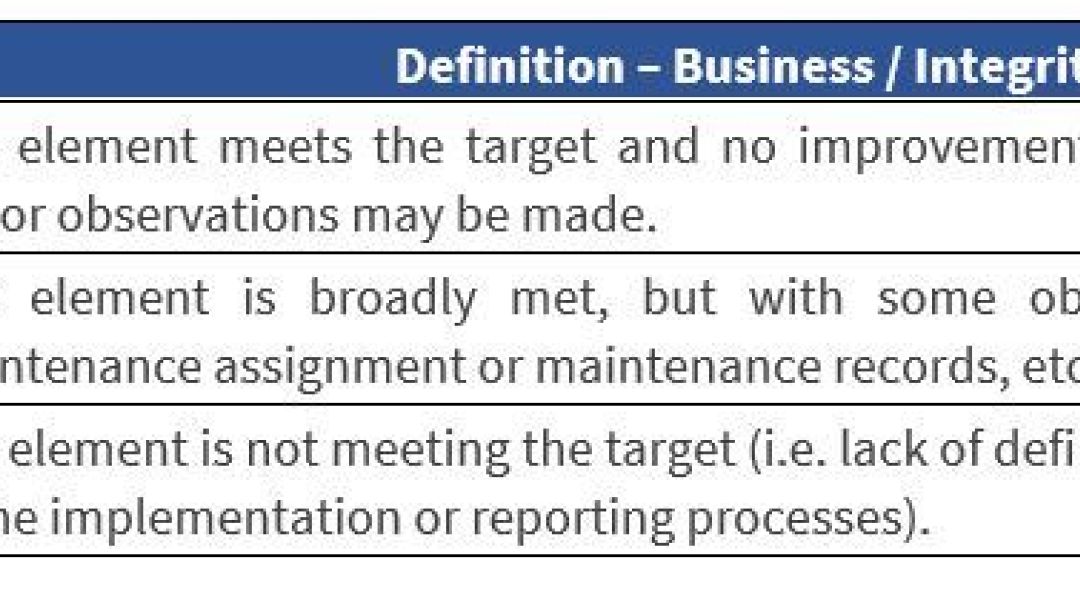
The impact
The degree of compliance with the requirements in the Safety Case was determined through a detailed document analysis and offshore inspection, and a detailed description of the findings was provided.
We delivered a documented independent assessment of the FPSO, which gives a better understanding of:
- the health of the integrity management system;
- an itemised listing of the criticality of each piece of equipment surveyed.
- A component integrity statement provided for each safety critical component. This statement provides information about the criticality, probability and consequence of failure; design and operations information, and location.
To ensure quick access to the health status findings for management, the findings were classified colour coding for each safety and environmentally critical element. These were: green, yellow, amber or red which indicated a health condition from 'no deficiencies' to 'require immediate follow up'
In the past asset owners relied on a full-scale survey of an offshore unit. However, this project showed that by making a selection of the critical elements, an effective health assessment of the unit is obtained which identified the effectiveness of the existing Integrity management process, with a minimised disruption of the operation on the offshore unit and at reduced costs.
Proof points
- Better understanding of the health and integrity of their management system
- Provided with an itemised list to display the degree of compliance for each piece of equipment surveyed
- The client can now plan for future inspections more effectively by focussing on the medium-high and high critical components
- Risks reduced through more effective inspections
- Costs reduced from not carrying out a full-scale survey
Testimonial
The team that completed the assessment of the FPSO was excellent. It was evident that they were indeed subject matter experts in their respective fields. All team members appeared well versed in industry best practices and relevant codes and standards. The international team from different backgrounds in the Oil and Gas industry was effective in completing the assessment.
All aspects of the onshore and offshore assessment were completed in a professional matter, and it was noted that the team spent their time on task and worked effectively together. The technical knowledge and understanding of the systems being assessed was evident, and the team was more than willing to discuss any identified problem areas along with what would be necessary to correct the identified problem. The technical expertise of the LR team (know, known as Vysus Group) was evident in all interactions.
This project was carried out by Lloyd’s Register (LR) Energy, prior to the strategic carve out of the LR Energy business in 2020, which is now Vysus Group.