Client
Major Oil and Gas Operating Company
Asset
New gas compression platform (FEED stage)
Location
Middle East
Client Challenge
For over 40 years, the Hazard and Operability (HAZOP) study process has remained largely unchanged, continuing to rely on human-driven assessments. While new tools and software have been introduced to address limitations, the core methodology has seen little transformation.
Vysus Group, and our technology partner, Kairos Technology, recognised an opportunity to digitalise the whole process and we developed HAZOP Assistant.
During the FEED stage of a new gas compression platform, our client sought to compare the performance of HAZOP Assistant, the digitalised HAZOP process (dHAZOP), with a previously conducted traditional HAZOP.
Key evaluation criteria included:
· Completeness of hazard identification, including coverage of causes and consequences.
· Consistency in risk ranking and application of severity/likelihood rules.
· Time and resource savings.
· Overall cost-effectiveness.
How We Helped
HAZOP Assistant, combines our deep risk analysis expertise within high-hazard industries with Kairos Technology’s game-changing AI technology to digitalise the HAZOP process.
We developed a strategic approach to assess and implement the HAZOP Assistant, following five key phases:
Preparation: A functional digital twin of the project was created using the HAZOP Assistant tool. Equipment libraries and the Multilevel Flow Modelling (MFM) programming language, a type of Explainable Artificial Intelligence (AI), were used. The modelling was built in one month with the support of two modellers.
Workshops: A set of rules for qualifying causes and their likelihood, as well as consequences and their severity, was introduced during the preparation of the digital HAZOP workshop sessions.
Site Assessment: MFM was used to analyse cause-consequence propagation in equipment, ensuring comprehensive hazard coverage.
Reporting: Delivered a comparative analysis of digital HAZOP vs. traditional HAZOP, outlining key benefits and areas for further enhancement.
On-going Support: Provided recommendations for integrating the digital twin with other safety studies such as Operational Risk Assessments (ORAs) and Failure Mode and Effect Analysis (FMEAs).
70%
Up to 70% of scenarios identified prior to HAZOP workshop
35%
35% time savings compared to traditional HAZOP
Powerful Results
- The application of the HAZOP Assistant produced significant benefits for the client:
- Up to 70% of scenarios were identified prior to the HAZOP workshop.
- Time savings of 35% compared with traditional HAZOP
- Traditional HAZOP workshops typically last 6 to 8 days, digital HAZOP workshop was completed in just 4 days while maintaining quality.
- Increased consistency: Automated risk ranking rules improved coherence and eliminated human-driven inconsistencies.
- Long-term value: The functional digital twin can be updated continuously, supporting risk reviews, training on the plant, and integration with other applications such as the Control Room Assistant.
- Comprehensive risk coverage: While the digital model generated extensive results, future enhancements will focus on refining data filtering for improved analysis.
Vysus Group's HAZOP Assistant demonstrated the potential of AI-enabled solutions to transform the HAZOP process, powering decision-making with deeper, more accurate insights, faster to power decision-making.
To explore how we can support your next HAZOP please email alfredo.haubold@vysusgroup.com or contact us here.
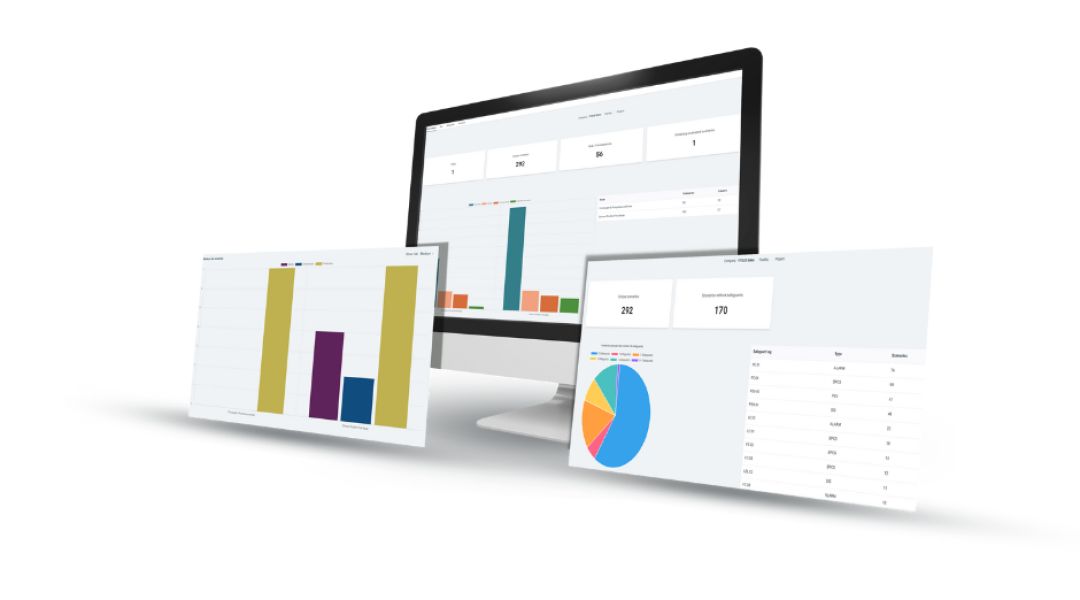
Related Services