The oil & gas and petrochemicals industries experience regular cycles of oil price and product supply. Sometimes these cycles are exacerbated by external factors like the COVID pandemic that has severely impacted the global economy and reduced global demand.
Both upstream and downstream operators are subject to these influences. Facilities are coming under increasing pressure to reduce costs while maintaining excellent records of safety and reliability. These dual expectations can only be met by carrying out the right maintenance and inspection activities at the right time. In fact, the best opportunities for reducing operating costs are by eliminating unplanned shutdowns due to equipment failure during operation and avoiding unforeseen repairs during turnarounds.
Updating RBI programmes can play a crucial role in reducing operating costs without compromising on safety and reliability.
Why refresh your RBI?
RBI programmes rely on historical data to predict future damage. They assume similar operating conditions and corrosion rates to set future inspection requirements. However, the past is not always a good predictor of the future, especially when there are changes.
In the current economic climate, both upstream and downstream operators are running at lower throughput rates. Some plants are using different feedstocks to adjust their yield profile and reduce costs. Each of these changes is a deviation from the assumptions of an existing RBI program. New process conditions can increase the rate of equipment degradation and may cause different damage mechanisms; therefore, RBI programs should also be refreshed to update the risks of equipment failure.
Updating RBI programmes doesn’t have to be as complicated as it may sound. Starting with high-risk circuits and specific areas where damage can be expected, can yield immediate benefits without the considerable expense of a complete review.
A holistic approach
RBI software tools generate inspection schedules based on input data. The quality of that data has a significant impact on the effectiveness of the RBI solution. Out of date plant information or missing inspection data has the potential to skew the software tool output. Using a trusted and experienced engineering partner and taking a more holistic approach could help to optimise any RBI program.
Vysus Group follows these four steps as a holistic approach for refreshing an RBI program:
- Review background information, including the existing RBI program.
- Gather updated process and operations data. Using actual process trends allows engineers to validate the underlying RBI assumptions and update them as necessary. Update design data for any plant modifications or feedstock changes.
- Reassess the Damage Mechanism Reviews (DMRs) by identifying corrosion loops and developing Corrosion Control Documents (CCDs). This step is critical to ensure that the underlying assumptions are correct before risk calculations are updated.
- Recalculate risks by updating upload sheets for RBI software with the latest DMR and CCD information as inputs.
The Benefits of Integrity Operating Windows (IOW)
Integrity Operating Windows define the operating conditions in which the RBI assumptions remain valid. Using IOWs, therefore, gives operators a warning when operating conditions are putting equipment at undue risk. Moving outside the limits introduces new damage mechanisms or raises the corrosion rates beyond acceptable levels. The greater the impact on risk, the more urgently action must be taken to bring the plant back within the IOW limits.
A quantifiable example of the use of IOWs is the susceptibility of heater tubes to creep damage. Skin temperatures less than 1000 F (538 C) keep the tubes outside of the creep damage mechanism. This upper limit effectively defines an IOW for heater tubes. Localised hotspots caused by flame instability or fouling that significantly reduces heat transfer can move a heater tube outside of the IOW. The impact of this on the life of the tube is shown in the graphs below.
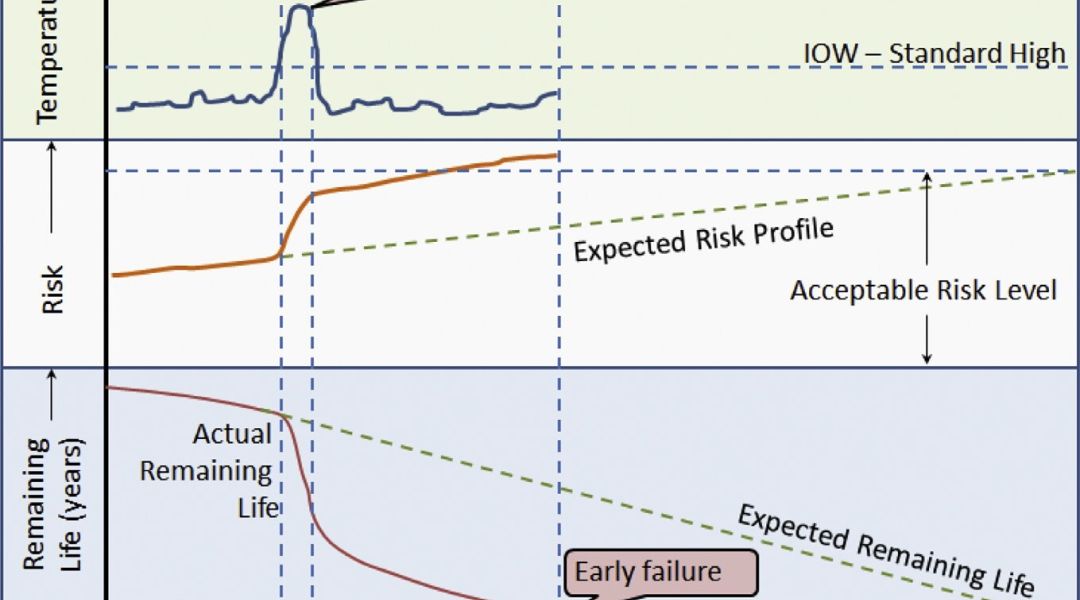
Figure 1: Visualisation of IOW - illustration of sulfidation damage in carbon steel piping
An IOW breach can be used to modify the inspection schedule for the heater. In this case a typical 4-year inspection frequency would result in a “surprise find” at year 8 with less than 2 years of remaining life. In a worst-case scenario, an earlier failure could result if damage is more aggressive or inspection is postponed for a year. Utilizing an IOW based alert system, it is then possible to bring forward the next inspection date for the furnace to measure the actual creep impact on the affected tube and take proactive correction action as needed.
Why Chose Vysus Group
Vysus Group was previously the Energy business of Lloyd’s Register. As such, we are a leading engineering and technical consultancy offering specialist risk management expertise across complex industrial and energy assets. Our track-record stretches back to the 1930s and covers a wide range of customers, equipment types and industries.
As an independent consultancy, Vysus Group is not limited to one specific set of software tools and models. Our engineers are adept at stepping into your organisation and using the tools already at your disposal. Also, our consultancy services span the globe allowing us to apply our broad expertise to each local situation.
Reach out to Vysus Group here, for more information about optimising your RBI program.