Inspection activities play a critical role in accurately diagnosing and preventing unexpected failures by adopting well-planned intervals. However, finding the most effective intervals has been a major concern across industries as a result of the potential costs and complexity of operations. In this article we discuss recent projects where quick wins were successfully identified when process safety valves were effectively managed.
When looking to optimise maintenance and inspection intervals, we often seek to find a good starting point to identify quick wins. These savings can often realise financial benefits to fund further optimisation activities and can identify the maintenance burden which allows the work to be programmed into the schedule. The purpose of this is to identify opportunities for improvement based on the hours spent on the maintenance activities. This often involves slicing and dicing the data in different ways, perhaps by the lead discipline of the work involved, by the current maintenance interval or by the equipment being maintained.
For example, in the graph below we can see that 980 hours a year are spent swapping out PSVs as part of an inspection program.
Often from a practical perspective, there are two main areas which need to be considered:
Time-significant time is spent on PSVs.
The failure history associated with PSVs is based on the pre-pop test results and can be readily collated and analysed.
The graph below illustrates the process involved in this analysis:
Valves are subdivided into logical types based on their fluid service. These typically include, hydrocarbon gas, potable water, seawater crude oil, lube oil etc.
The pre-pop tests are examined and categorised as shown below:
failed safe (valve leaked or lifted at <90% of the set pressure)
passed (lifted at 90 to 110% of set pressure)
failed dangerous (valve failed to open or lifted above 110% of set pressure)
At the same time, the operating history as evidenced by the pre-pop test is calculated for each service fluid. If a valve has no pre-pop test, then no operating history is recognised. The purpose of the review is to set an inspection interval which is used to detect a hidden or dangerous failure when the valve fails to operate on demand. By setting a reliability target for the group, only the dangerous failure rate is used in the computation. It is common practice to use a target reliability of 90% for a non SECE valve and 95% for a SECE valve. A typical result is shown below:
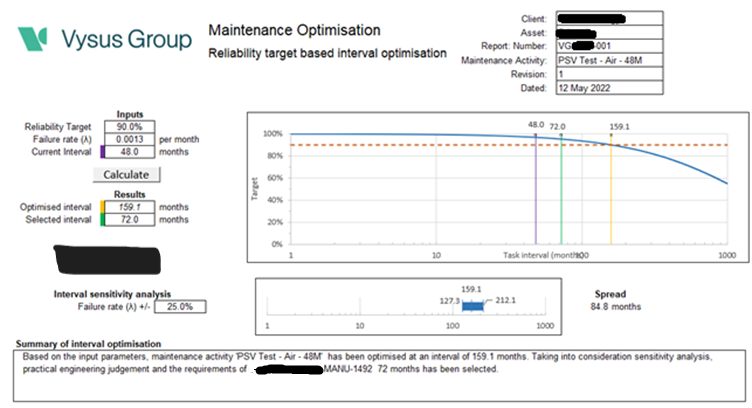
Our Asset Management team is currently in the process of conducting a fourth review for a number of platforms for one of our clients. In this case, it is clear that the assets in question had changed hands quite a few times and had been under separate ownership in all of the previous reports. The process for setting the inspection intervals remained constant throughout the change of ownership of the assets. Due to the successful review, our client has now adopted a reliability target approach to setting their inspection intervals across all of their assets and have included this process in their PSV maintenance manual.
Building on this project success, our team recently completed a review on an asset with over 1000 PSV valves. This asset was a mature platform with the inspection intervals being regularly updated rather than fixed. In the past a qualitative approach had been used by our client to determine maintenance intervals applied to PSVs based on a decision tree which incorporated historic testing results and other risk factors. That approach was risk-based, but qualitative in that a deterministic link between testing interval and risk was not available.
The results of this review can be seen in the graph below which shows a clear shift in maintenance intervals to the right across all of the service groups:
As the average amount of PSVs on air service were being changed out each year, this resulted in a yoy reduction from 120 to 82. These results were achieved with approximately six weeks of work. It should be noted, of course, that the purpose is to set a maintenance interval to reach an agreed reliability target so the valves have their inspection intervals reduced. There are also a number of checks and balances when applying the interval updates to individual valves including:
- putting a limit on how much the original limit can be extended
- don't extend the interval beyond the caped maximum for each group
- don't adjust the interval of an individual valve where the most recent test recorded a dangerous failure
A significant benefit of this process is that should there be a requirement for an interval deferral as any impact on the reliability achieved from the change can be readily calculated. As such, the overall level of protection analysis can be easily updated and assessed as part of the operational risk assessment.
If you would like to find out more about how we can help you effectively optimise your operations please contact Gordon Ellis, Maintenance and Reliability Team Leader gordon.ellis@vysusgroup.com